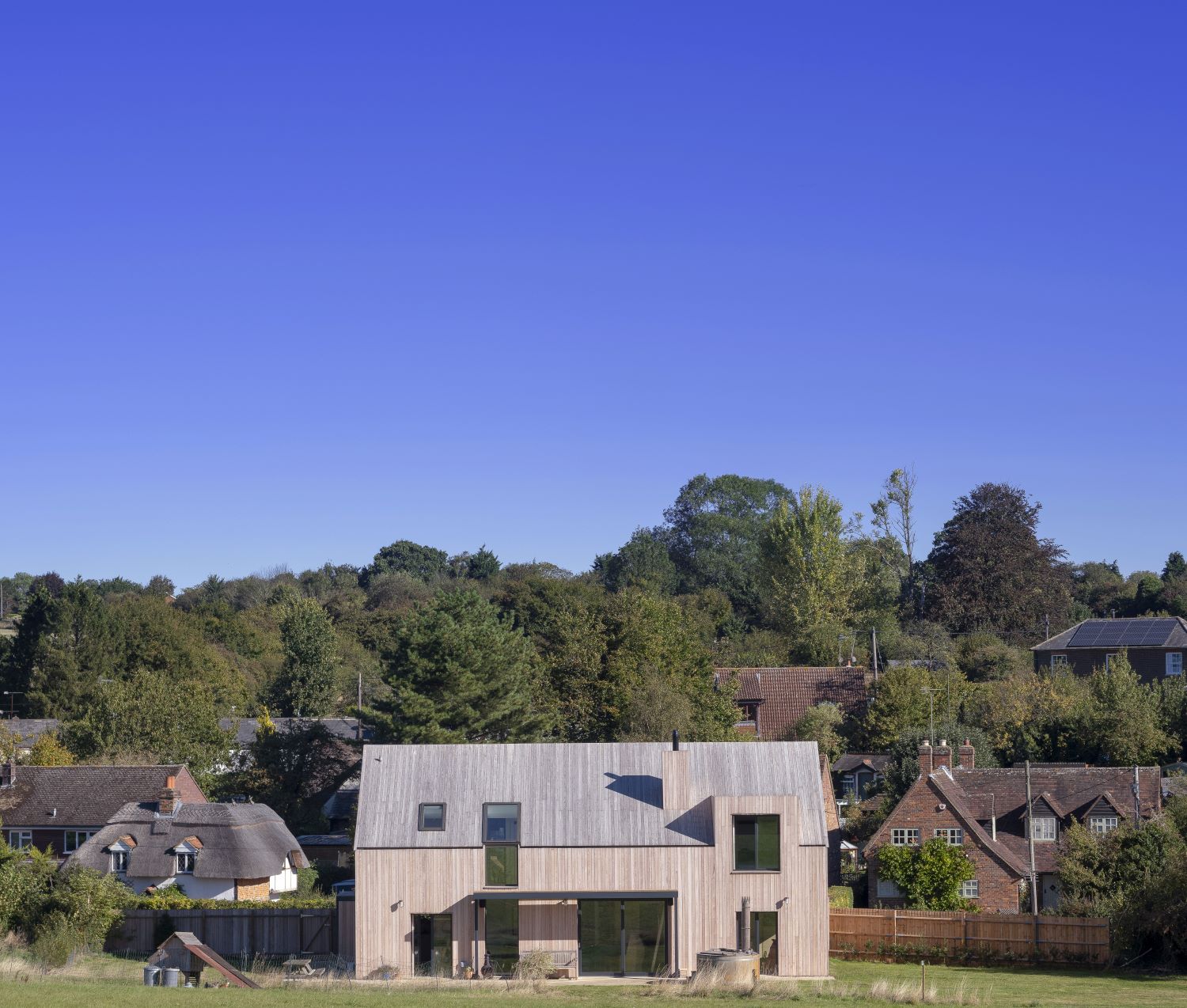
This article is for anyone who is considering adopting the Passivhaus standard for their project and wants to find out more about the costs involved.
Passivhaus is the recognised standard in delivering low-energy, comfortable and healthy buildings, whether these are homes, schools, universities, offices or any other building type. This article will focus primarily on the costs associated with Passivhaus. If you would like an overview of the Passivhaus standard please do refer to the summary by Tate+Co Architect Hannah Pinsent here.
Why Passivhaus projects can cost more to build
Building to the Passivhaus standard requires a particular approach to both design and construction in order to meet the energy use and air tightness targets. Whilst these targets are becoming more familiar to the construction industry, they are still the ‘gold standard’, and as such can cost more than a ‘business as usual’ approach.
Below are the main reasons a Passivhaus project may increase the overall project cost:
Passivhaus design – Costs during the design stage associated with additional detailing and modelling, including using Passive Haus Planning Package (PHPP) software. This could either form an additional part of your architect’s scope or you could appoint a separate specialist consultant.
Wall and roof structures – The majority of the building’s heat loss will be through the external walls and roof, (with the remainder being lost through the ground floor). These elements need to be carefully designed and constructed to ensure the building is ‘wrapped’ in insulation and that there is no, or very minimal, thermal bridging to limit the heat load to no more than 15 kWh/(m²yr).
Windows and doors – These will need to be triple-glazed, high performance windows and doors. Windows require a Uw-Value of <0.8 W/m2K, one way of ensuring this is to use Passivhaus certified products, although this is not a requirement. Due to their specialist nature these can contribute to a significant portion of the overall costs.
MVHR – A Mechanical Ventilation Heat Recovery (MVHR) unit wseill be required and whilst these are fairly standard across the industry there are more stringent requirements for Passivhaus MVHR units.
Site supervision / QA – Passivhaus buildings sometimes require additional time on site to check that the building is constructed as drawn especially at junctions and openings in the external fabric. Additional time may also be required to ensure the building is very air-tight to achieve the target of 0.6 ACH, (air changes per hour) @ 50 Pascals.
Certification – At the end of construction a Passivhaus certifier will need to inspect the building and issue a certificate. This carries a relatively modest cost however it will need to be carried out by an independent party.
How much will this all cost?
It is important to benchmark the costs of delivering a Passivhaus project against a non-Passivhaus project to get a clear picture of the additional costs. The Passivhaus Trust, who promotes the use of the standard within the UK, carried out a comprehensive study in 2018 into the costs of adopting this approach.
Their conclusion, in 2018, was that it would add approximately 8% to the overall construction cost.
The study also looked at historic data, going back to 2010 when Passivhaus projects first started emerging within the UK, and reported that between 2010 and 2015 the same approach would add an additional 15-20%.
Finally, the report concluded that based on construction trends, an increased availability of high-quality materials, products and, most importantly an increase in skills and knowledge, they forecasted that by 2020 the additional costs would be around 4%.
A further study, carried out by Sustainability Consultants AECOM in 2021, concluded that additional costs as a result of adopting the Passivhaus approach saw only a modest increase of 0.9% of overall construction costs.
The chart below indicates the additional costs of Passivhaus over the last nine years from 2015 to 2024.
How to build Passivhaus without additional costs
There is a clear downwards trend in costs associated with building to the Passivhaus standard, which is hugely positive for the industry as a whole, as it should encourage more projects to adopt the approach. This trend is largely driven by increased awareness, skills and specialist knowledge, all of which have become more relevant in the last 15 years as sustainability targets and net-zero ambitions become higher priorities.
However, if you are thinking of building using Passivhaus you will still need to take some essential steps to ensure your project does not attract additional costs. The key steps are:
Early planning – Key design decisions need to made at the outset, such as massing, form factor, orientation and indeed whether this is the right approach for your project. For example, a heavily trafficked building with large openings is unlikely to meet the air-tightness requirements.
Getting the right team on board – You should appoint designers with the appropriate skills and experience who can guide you through the process. This applies to builder’s too; employing a contractor who understands the philosophy is key.
Identify value engineering early on – Most projects will have to undergo some form of value engineering at some point; this needs to be tackled early on to avoid costly compromises later on.
What will happen next?
The clear downward trend in additional costs for Passivhaus is heading towards zero. Factor in increasing energy costs and any additional build costs will have a shorter and shorter payback period over the lifetime of the building. Any residual costs could be offset by the potential premium Passivhaus projects could attract on the market.
It’s also worth noting that, regardless of additional costs, a Passivhaus building will simply be a nicer place to live, work, study etc than the equivalent non-Passivhaus building which, at the end of the day, is the most important outcome.
Further Reading
– Passivhaus Trust Costs and Benefits
– AECOM “Debunking the myth that Passivhaus is costly to achieve”
Andrew Baker-Falkner
Director
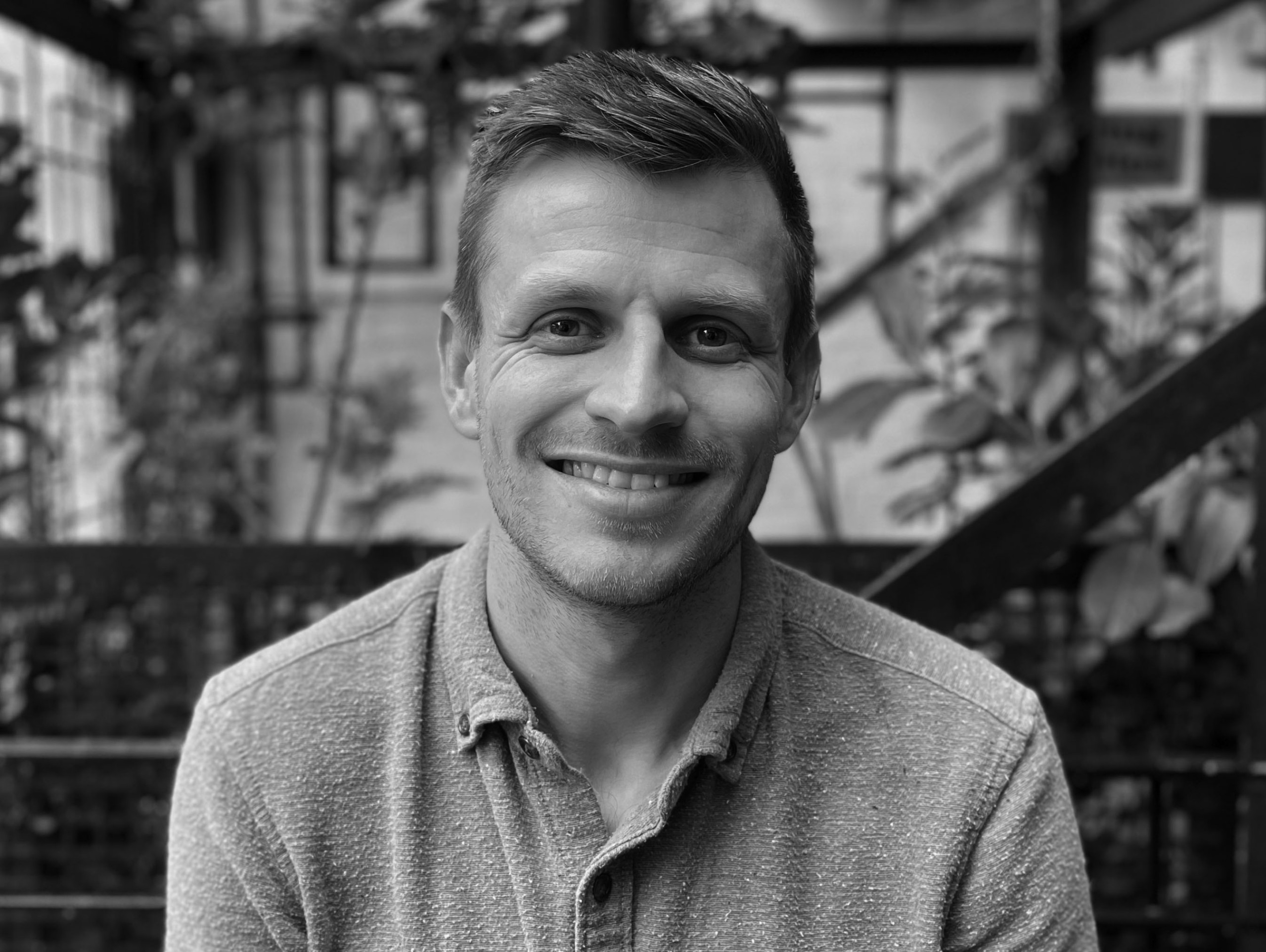
Andy is a Director at Tate+Co and joined the practice in 2014. He has extensive experience at leading multi-disciplinary teams and complex projects to successful outcomes. These projects cover a range of scales, sectors, and locations. Notable projects include Creative Centre for York St. John University and Townsend Building for Cranleigh Preparatory School, which Andy led from conception to completion.
Andy has also delivered masterplans, community projects and housing and regeneration schemes for a multitude of clients. Whilst working across a broad range of projects, Andy has a particular interest in education and the positive benefits of connecting learning spaces with nature and has shared these learnings as a speaker at the Education Estates Conference and the Structural Timber Conference.